Documentation needed to start a candle business.
What documentation is required to open a candle business. How to start producing soy candles. What is needed to start producing soy candles. Documentation compliant with REACH and CLP. Documentation needed for candle production.
For several years, I have been involved in creating technical documentation related to the chemical industry. I often encounter similar questions, to which I will try to provide brief answers in this post.
The post is for illustrative purposes only and does not constitute legal advice. The completeness and correctness of the documentation are the responsibility of the substance manufacturer. The aim of the post is to systematize information and address the most frequently asked questions. It does not provide precise advice on how to conduct comprehensive documentation but serves as an overview.
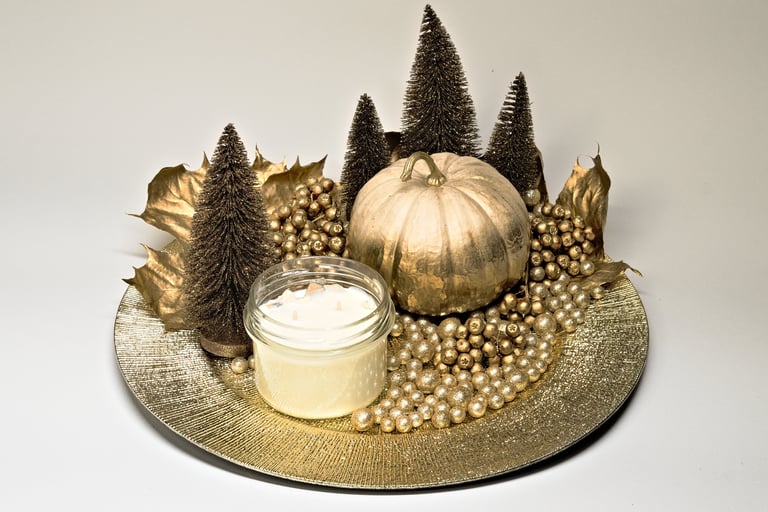
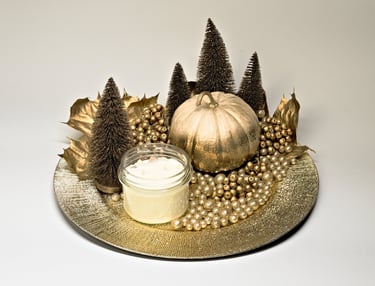
How to start making candles?
First, we need to determine what kind of candles we want to create. There are many options. We can add fragrance oils, dyes, additives, create them with different waxes such as soy wax, beeswax, paraffin wax, coconut wax... The purpose is also essential - massage candles are cosmetic products. Here, a more extensive documentation is required. This post refers to classic candles. Candles resembling food are also a separate topic, which I will not address here.
Above all, candles should be treated as chemical mixtures (REACH), subject to classification and labeling according to Regulation (EC) No 1272/2008 CLP by the European Parliament and the Council.
Once we have determined what we want to create:
For odorless candles consisting solely of wax
Here, the situation is quite simple. It is enough to have a wax safety data sheet (the seller is obliged to provide it upon request) and develop the temperatures at which we should work. By creating single-component candles, we are not creating a new mixture; we are not its manufacturer.
For any multi-component candles
If you add dye, fragrance, any additives to your candle - you are creating a multi-component mixture, and you are its manufacturer.
ALWAYS, you must have a mixture classification done. Without it, you do not know if your mixture complies with the law. Also, pay attention to temperatures during candle making, especially the temperature of adding fragrance oil and dye. There are many factors to consider, which I will gradually develop in subsequent posts. This one can be seen as an introductory overview.
How to check if a candle is "safe"?
I'll clarify right away, I'm putting the word "safe" in quotes here because a candle is not generally a safe product. But I think I don't need to elaborate on that further (if necessary, let me know).
Classification is the basis for creating any chemical mixture, whether it's soy candles, paraffin candles, cosmetics, etc.
Classification is done according to Title II of the CLP Regulation Articles 5-16. Without classification, we don't know if the product complies with the CLP Regulation that applies to us as manufacturers of a chemical mixture.
You can read more about it, among other things, under this link: https://echa.europa.eu/support/mixture-classification/where-do-i-start
The classification I'm referring to is the classification of mixtures by calculation method, based on the content of hazardous ingredients.
Classification must always be done when creating a new mixture, regardless of whether you want to make candles just for yourself, sell them only among friends, or set up a shop and sell them to a wider audience.
First of all, contrary to what many people think, classification is not a document. When creating a classification, I always check the correctness of the component documentation and make sure there are no exceedances. In the described case, it is the balance of the mixture.
What will be useful?
Safety data sheets for components (the seller is obliged to provide them upon request),
IFRA certificates for fragrance compositions,
Recipes.
The first thing to do is to check whether the safety data sheets for components comply with the most current requirements of the REACH directive (this is not necessary from the point of view of CLP, but REACH regulates how the safety data sheet should look, so it is worth verifying it at this stage (or earlier)).*
* NOTE: As of January 2023, safety data sheets should be prepared in accordance with the latest safety data sheet template specified in Regulation (EU) 2020/878. All previous safety data sheets that do not take into account these changes can be used until December 31, 2022.
You can find the content of the REACH directive under the link: https://echa.europa.eu/web/guest/regulations/reach/legislation
Based on the recipe and safety data sheets, the chemical balance of the mixture is calculated. In the case of calculation classification, attention should be paid to two definitions appearing in the CLP regulation::
cut-off value,
concentration limit.
I urge you to pay attention while reading the regulation.
After classification, we also find out what hazard pictograms we must place on our product according to the CLP Regulation.
You can find the content of the CLP regulation under the link: https://echa.europa.eu/regulations/clp/legislation
More on pictograms a little further down.
What if there is an exceedance in the classification?
During classification, it may turn out that your mixture exceeds concentration limits.
In that case, you can take one of the following steps, of which I definitely recommend the first:
Changing the recipe
You will probably need to reduce the amount of fragrance oil or dye. The person performing the classification for you will inform you how the recipe for your components should look like.Registration of the substance as hazardous
If you do not want to change your recipe, but there are exceedances on it, you are obliged to register the mixture in the PCN, assigning it a UFI number at that time. You can read more about it under the link: https://poisoncentres.echa.europa.eu/documents/1789887/1803644/ufi_what_it_means_en.pdf/576a9a82-c352-b5b3-df73-e763da37e559 and in the CLP regulation itself.
Apart from the classification topic: it is good practice to check the REACH candidate list. Very rarely, but there are cases, for example, of lead compounds in dyes.
List link: https://echa.europa.eu/candidate-list-table
When do I need to have a safety data sheet for my candle?
A safety data sheet is not always required.
Just as classification is mandatory for every product, a safety data sheet is not needed in every case.
A safety data sheet is required when:
you sell the product on a VAT invoice,
you sell the product for further resale,
the mixture has been classified as hazardous.
I absolutely recommend having a safety data sheet for every mixture. It is a document informing us about safety and, in my opinion, we should also treat it as a document that, if well prepared, also protects the mixture manufacturer.
There are cases when there is no obligation to present a safety data sheet (SDS). That means if:
you sell products only to private individuals, your mixture is not classified as hazardous - you are not obliged to provide a SDS,
you sell candles only among friends, your mixture is not classified as hazardous - you are not obliged to provide a SDS,
you sell candles only among friends, but you have received a proposal from another entrepreneur (e.g., a shop, a florist, etc.) to sell your products - a SDS is required to be able to sell them in the described shop, florist or other place,
you sell candles in your shop and issue a VAT invoice for them - a SDS is required,
the mixture is not classified as hazardous, but it exceeds the concentration limits used to disclose the components of the mixture classified as sensitizing - a SDS is required,
the mixture is classified as hazardous - a SDS is required,
you sell candles to entrepreneurs; you sell candles for further resale - a SDS is required.
Would you like to receive more content like this?
Subscribe to our newsletter.
What pictograms should I place on the candle?
As I mentioned before: Candles should be treated as chemical mixtures (REACH), which are subject to classification and labeling according to Regulation (EC) No 1272/2008 CLP of the European Parliament and of the Council.
Whether and what pictograms we should place at the beginning will result from the classification conducted and the provisions of the CLP regulation.
Each pictogram indicating the type of hazard should occupy at least one-fifteenth of the minimum area of the label intended for information required under Article 17 of the CLP, however, its minimum area cannot be less than 1 cm2. The minimum dimensions of labels and pictograms are provided in Table 1.3 in Annex I to the CLP.
Detailed information on labeling can be found in Title III of the CLP Regulation, Articles 17-33.
Pictograms intended for printing can be downloaded from the following link: http://www.unece.org/trans/danger/publi/ghs/pictograms.html
Additionally, there is a standard EN 15494:2019 Candles. Product safety labels, which will inform you how the label for candles should look like and how to place pictograms.
The content of the standard can be found at the following link: https://www.en-standard.eu/bs-en-15494-2019-candles.-product-safety-labels/
Who can issue chemical documentation?
As for the classification - it can be done by anyone, but one should have appropriate knowledge in the field of chemistry and be familiar with the provisions of regulations.
As for the preparation of the safety data sheet, the person doing this should have extensive knowledge of chemistry. Just having a degree in chemistry might not be enough to prepare a good sheet. It is worth noting that this person should undergo specialized training. According to Commission Regulation (EU) 2020/878 Annex II Part A 0.2.3:
"The safety data sheet shall be prepared by a competent person taking into account the specific needs and knowledge of the users of the safety data sheet, to the extent that they are known. Suppliers of substances and mixtures shall ensure that such competent persons undergo appropriate training, including refresher training."
However, it should be remembered that the responsibility for the documentation always lies with the manufacturer, importer, or distributor of the chemical mixture. Therefore, it is worth checking the qualifications of the person to whom we entrust the preparation of the documentation.
*This post was informative in nature, but it does not present all directives related to chemicals. A list of other regulations and directives, the knowledge of which may also be useful when issuing documentation, includes:
Directive 2008/68/EC concerning the inland transport of dangerous goods
Directives 2000/39/EC, 2006/15/EC, and 2009/161/EC on occupational exposure limit values
Directive 89/686/EEC on personal protective equipment
Legislation on plant protection products and biocidal products
Directive 98/24/EC on chemical agents
Directive 2004/37/EC on the protection of workers from the risks related to exposure to carcinogens or mutagens at work
Directive 92/85/EEC on measures to improve safety and health at work for pregnant workers, workers who have recently given birth, and workers who are breastfeeding
Need help with documentation?
I am conducting classification,
I am creating safety data sheets,
I provide individual consultations on documentation for candles.